本コラムは、ダイヤモンド社発行の「DX戦略の成功のメソッド~戦略なき改革に未来はない~」の第5章の抜粋記事です。
試し読み
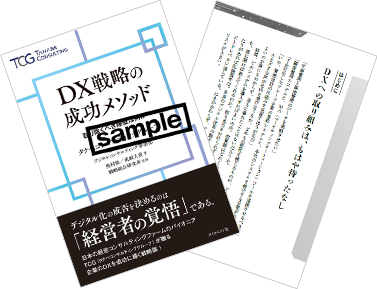
オペレーションDX
(1)成果獲得のポイント
① 4つの成功ポイント
オペレーションDXとは、バリューチェーン上の開発・設計・調達・生産・物流といったオペレーション領域で、アナログとデジタルの融合により突出した差別化ポイントを実装し、現場の生産性やエンゲージメントを高める労働環境づくりを経て、事業収益の向上を目指すものだ。このオペレーションDXで成果を上げるポイントは4つある。
1つ目は、バリューチェーン上の開発・設計・調達・生産・物流において、どの機能(または工程)で「突出」するかを意思決定することだ。「現場で何ができるか」という視点でスタートすると、省人化や省力化といった現場生産性の向上にとどまってしまう。なお突出した差別化ポイントは、足元の競争環境のみならず、10年先の自社が戦う想定マーケットから見て検討することをおすすめしたい。
2つ目は、経営ニーズと現場ニーズを接続するコーディネーターの配置である。経営者が実現したいことや知りたい情報と、現場のオペレーターが実現したいことや知りたい情報は異なる。どちらかに偏るとデジタル実装は失敗に終わる。このため経営ニーズと現場ニーズの接点づくりと、接点で実装するデジタル技術をコーディネートすることが重要である。このあたりの対応はシステムベンダーでは難しく、コンサルティング会社やデジタル実装サービス会社など外部パートナーと連携することが主流となっている。外部のパートナーと連携すれば、DXで実現したいビジョンを可視化でき、デジタルへの投資効果を実装前に検証もできる上、DXでもたらされるメリットも社内で共有しやすくなるからである。
3つ目は、アナログとデジタルの融合による取り組みである。オペレーション領域すべての工程をデジタル化することは現実的ではない。技術的に可能であってもデジタル実装の数に比例してイニシャル投資、ランニングコストがかかる。このため、突出した差別化ポイントにしていく工程を中心に、まずアナログによる業務改革、つまりモノとデータフローの整流化と効率化を図り、同時にデジタル化を設計・実装していくとよい。
4つ目は、エンゲージメントが高まる労働環境づくりという観点を持つことである。肉体的・精神的にきついといわれる労働環境は、労働者の年齢を問わず敬遠される。ウェアラブルカメラやスマートウオッチなどのデバイスを装着して働き、デジタル活用により効率的に成果を追求できる労働環境が整備されるとQCDS、つまり、品質マネジメント・コストマネジメント・納期マネジメントおよびサービス水準が向上するにとどまらず、そこで働く人たちのエンゲージメントが高まるという効果がある。
ゲーミフィケーション、さまざまなゲーム的要素として生産高やコストダウン額、改善提案件数などの成果をデジタルで可視化することで、現場のモチベーションアップやエンゲージメント向上へとつながる。デジタル実装の目的を省人化・省力化とせず、エンゲージメント向上や採用強化を目的とする企業もあるほどだ。
② 現状認識
オペレーションDXを具体化する上で重要なカギを握るのが、外部環境・内部環境の「現状認識」である。
まず外部環境では、ベンチマーク企業のオペレーションDXがどの程度進んでいるかを把握する。例えば、設計図と現物によるすり合わせを繰り返す開発設計工程をデジタル化し、リードタイムを大幅に短縮した事例などである。DXで日本より先行するEUや米国など海外のベンチマーク企業を視察したり、オペレーションDXに関連する展示会を見学したりして情報収集しておきたい。その際、必ずしも同業界である必要はない。異業種の事例を取り込んでイノベーションを起こした例は多い。
次に定量面と定性面の両方から内部環境を把握する。定量面では、バリューチェーン各機能における生産高やコスト、利益を可視化してどの工程で稼ぎ、どの工程で損失が出ているか、収益性を押さえる。さらに1人当たり生産高や1日当たり設備費などの生産性指標も把握する。収益性と生産性を数値で可視化すれば、どの工程を突出させ、改革すべきかが見極めやすくなる。可視化した数値をベンチマーク企業やライバル企業と比較できるとなおよい。定性面については【図表5-18】をもとに課題を押さえる。
横軸は現場に投下される経営資源(人や設備、手法など)を、縦軸は現場で管理する要素(製品や品質、原価など)を表している。押さえるべきはモノとデータフロー、オペレーション上の業務・システム運用面である。例えば生産工場において、原材料・仕掛品・完成品在庫の工程間移動が現物引き渡しのみか、紙伝票による処理がなされているか、バーコードリーダーでデータ処理されているか。またタイムリーな在庫情報の把握が可能か否か。もしなされていない場合の原因は何かを具体的に特定する。この特定作業には多くの時間と工数がかかるが、ここを省略するとデジタル実装の前段階となるシステム・デバイス要件定義を見誤り、結果としてデジタル実装が失敗に終わる。現状認識は的確な要件定義のためにも具体的に押さえる必要がある。
③ 工程別DX戦略のポイント
オペレーションDX戦略は、何を目指すのかを明確にする必要がある。推進目的としては次の3点が挙げられる。
1点目は、業務プロセスを可視化し、データを一元管理することでタイムリーな経営判断ができる仕組みの構築。2点目は、バックオフィスを含めた業務の軽量化を図り、非付加価値業務に充てる時間を付加価値業務へ再配分する。3点目が、デジタル化でカバーしきれない業務はアナログで改善を図ることである。
また、オペレーションDX戦略は全体視点から工程別にブレークダウンすることが大事だ。各工程がそれぞれ目の前の業務改善だけを進めると部分最適に陥り、前後工程の生産性を極端に落としたり、余分な業務が増えたりする恐れがある。単なるオペレーションの改善ではなく、自社の強みの発揮を目指して事業のやり方を根本的に見直すことだ。
ここでは、オペレーションDX戦略で重要な工程である調達、生産、物流の各DX戦略の重点ポイントを解説する。
● 調達DX戦略
「利は元にあり」といわれるように、原材料の品質やタイミングによって生産性や在庫状況、歩留まりが大きく変わる。仕入れの巧拙は企業の利益を大きく左右するだけに、調達業務のDXはオペレーションDXのなかでも利益向上に直結する取り組みとなる。
業種・業界によっても異なるが、調達計画は通常、「PSI計画」(Product =製造部門の生産計画、Sales =営業部門の販売計画、Inventory =物流部門の在庫計画)をベースに立案される。ERPで一元管理と情報共有化を行いつつ、担当者の経験と勘に頼るのではなく、AIを導入し過去のデータのパターンから欠品しないぎりぎりの最低ロットを予測、高い精度の最適数量調達を行う。
ただ、AIの分析結果をそのまま自動発注につなげるのではなく、人がチェックするべきである。AIはデータを分析して「判断」することはできるが、〝決断〟はできない。現在は国際政治、自然環境、人手不足、エネルギー需給、為替相場、物流動向など、さまざまな要因で原材料価格が変動する時代である。不確定要素が増えるなかで安定的な原価管理を実現するには、次工程へ臨機応変にバトンをつなげる調整役が必要だ。調達DXは、データ活用のデジタル化を進める一方、人が介在すべきアナログ領域も必要である。
例えば、新規仕入れ先の開拓は重要な調達機能の1つである。今、ウェブ上には仕入れ先の開拓につながる多くの情報が散見される。将来を見据えた仕入れ候補先をデータとして蓄積し、必要に応じて速やかな検索ができる状態を構築したい。特に、販売に注力している企業は自社サイトにマーケティングページを設け、MAなどの機能を入れていることが多い。したがって、興味がある製品や原材料を検索すると、その企業から情報が自動的に収集できることも多い。
一方、アナログ領域ではリアルの展示会へ常に足を運んでほしい。さまざまな企業が最新の情報や製品を発信している。なかにはネット上で情報発信していない技術を知ることができる場合もある。今必要ではないが、将来活用できる情報や企業が出展している可能性もあり、デジタルと併せてアナログでも情報収集することが大事である。
● 生産DX戦略
生産現場のデジタル化が進む一方、紙の手書きデータをタブレットに手入力する工場も見受けられるなど、アナログ文化が根強く残る現場も少なくない。生産をスムーズに進めるためにも、デジタルを活用し、精度の高い生産計画を策定して生産状況を可視化するとともに、問題をいち早く察知できる仕組みを構築する必要がある。
生産工程のデジタル化を通じ、いかに企業価値を高めるかという視点が重要だ。デジタル化できる工程を見極め、費用対効果や優先順位を明確にし、省人化を進めることでゼロからプラスへと転化する。例えば、需要予測や販売計画からAIが生産計画を自動計算するシステムを導入したり、IoTで人の手作業を極力デジタル化して作業の余剰時間を付加価値業務に再配分したりするといったことである。
同時にマイナスをゼロやプラスに変える視点も必要だ。非効率な生産活動の発生要因は、設備トラブルや手待ちなどの停止時間である。設備が止まってから対応するようでは遅い。AIやIoTを活用すれば、現状の可視化だけでなく〝将来の可視化〟も可能である。設備故障の予兆管理や製品不良の発生予測により工程内での品質安定化を図り、人の目や感覚に頼ることなく手戻りを減らして直行率を上げる。
もっとも、生産現場ではデジタル化だけで効率化が図れない領域もある。5S活動やからくり改善(簡単な機構や仕組みを使って負荷軽減や効率化を図ること)などアナログで課題解決を図れる工程が存在することも事実であり、デジタルとアナログのバランスをとることが大事である。
● 物流DX戦略
生産活動が最適化されても、納品が不適切だとすべての努力が無駄となる。いわば物流は、自社の存在価値を発揮して顧客満足度を上げる最後の砦といえる。一方、物流部門は深刻な人手不足に直面している企業が多く、最もデジタル化が迫られている領域である。特に最近は、消費者ニーズの多様化や在庫リスクの低減、品切れ防止などへの対応から小ロット多品種生産・多頻度小口配送が求められる半面、SDGsの観点で環境負荷の低減や労働環境の改善も必須事項となっており、DXへの取り組みが欠かせない状況となっている。ところが、最終的には顧客のもとへ人の手で運び、積み下ろしせざるを得ない労働集約型の業務であるため、デジタル化が遅れているのが実態である。
ただ、荷姿や梱包サイズが明確であれば、デジタルを活用して効率的な輸配送が可能である。例えば、適切な荷姿をシステム化し、梱包サイズなどを自動計算して最適な保管方法や輸送方法につなげている企業がある。また、業界の垣根を越えて、トラック便(帰り便)の空きスペース情報を複数企業で共有し、合い積み輸送を行うケースが増えている。自動倉庫や無人搬送システム、ICタグを導入して省人化、省力化、ミス軽減につなげる企業も多い。
オペレーションDXは複数の工程にわたるため、各工程の目的を明確にし、「どの領域で尖ったDXを推進するのか」、その費用対効果も考慮した上で優先順位を決めることが大事である。そして何をデジタル化し、どれをアナログ的な改善でオペレーションするのか。併せて属人作業を排除し、標準作業へと進めることで効率的なオペレーションDXを実現できる。また、オペレーションDXは各工程の現場を熟知したメンバーを中心にボトムアップ型で進められることが多いが、往々にして部分最適に陥ってしまい、結果として全体不最適に終わるケースも少なくない。したがって経営トップのリーダーシップ発揮が重要である。現場を熟知したプロジェクトメンバー、全体最適のアドバイスができる第三者(コンサルタントや専門家)、社内調整と意思統一を図る経営トップの三位一体で推進していくことが望ましい。
(2)【実装事例】HILLTOP(ヒルトップ)/二四時間稼働の無人工場
ドイツが2011年に製造業の革新を目指す産業政策「インダストリー4・0(第4次産業革命)」を発表して以降、IoTやビッグデータを活用して無人化工場の実現に挑む動きが世界的に広まった。製造工程の自動化率75パーセントを達成したドイツ・シーメンスのアンベルク工場がその先進モデルとされている。しかし、それより以前の1980年代に無人化工場を目指し、システムを構築した会社が日本にある。アルミ切削加工メーカーのHILLTOP(本社・京都府宇治市)だ。同社では加工技術・作業工程を最適化・データ化・標準化し、24時間無人加工を実現。さらにはリピート品であれば最短3日以内の短納期、1個からの多品種少量生産にも対応するという、ものづくりの常識を覆すイノベーションを起こした。
① 企業概要
HILLTOPは1961年、「山本鉄工所」として京都市南区に創業。アルミ切削部品の試作品加工やFA(ファクトリーオートメーション)・医療機器などの装置開発を主力事業としている。取引先は国内のさまざまな業種の上場大手メーカーやベンチャー企業であり、米国法人ではウォルト・ディズニー、NASA(米国航空宇宙局)からも受注するなど幅広い。工場では5軸マシニングセンターなど約20台の工作機械が黙々と24時間無人稼働している。
社員約140人中、製造部所属は約40人。そのうち機械オペレーターはほんの数名で、大半はオフィスでNC(数値制御)工作機械を稼働させるための加工プログラムを組むなど、デスク作業を行っている。オフィス内部は部署ごとの間仕切りなどもなく、八角形にデスクが配置され、中央にはすぐ打ち合わせができるように円卓が設置されている。
同社で生産される製品は、自動車・航空・医療機器・ロボットなどの精密機器部品から、ミュージシャンのマイクスタンドに至るまで多岐にわたる。また他の加工メーカーが嫌がる、いわゆる「一品もの」「試作品」も多く、受注の約8割が1、2点の単品もので、1カ月に約3000種類の加工を行っている。しかも、これだけの多品種少量の製品を新規5日以内、リピート品は3日以内という短納期で供給しているのが大きな特長だ。2014年には米国法人を設立し、カリフォルニア州アーバインにヘッドオフィス・工場を設置したほか、テキサス州にオフィス(2021年)を開設している。
2022年には、クラウドエンジニアリングサービス「COMlogiQ(コムロジック)」を開発し、サービス提供を始めた。このサービスはユーザーが設計データ(3Dデータ)をクラウド上にアップロードして穴・公差指示を行うと、AIによって工程設計・プログラミングが行われ、NCプログラム(工作機械稼働用データ)と加工手順書(調達する材料のサイズ、使用する治具、材料のセッティング位置・方法など)が自動生成される仕組みだ。このサービス提供を通じて、人手不足や技能継承、事業承継などの製造業全体が抱える課題の解決を目指している。サービス提供方式は月額固定利用料に従量課金というサブスクリプション型を採用した。
熟練職人が暗黙知として蓄積してきた加工技術を最適化・データ化し、誰でも使用可能な形で共有できるように標準化を実現したことが高く評価され、2023年に「データガバナンス賞」(主催/一般社団法人日本データマネジメント・コンソーシアム)を受賞した。
② オペレーションにおける課題
創業時の同社の祖業は「鉄工所」であった。現社長・山本勇輝氏の祖父が家族3人で創業し、自動車メーカーの孫請けとして来る日も来る日も「丸物」と呼ばれる自動車部品を油まみれになって作り続けていた。全売上げの80パーセントを取引先1社が占めており、その取引先次第で受注がゼロになる可能性があるという「受け身」のビジネスモデルであった。
さらに毎年5パーセントのコストカットを要求され、受注を失うことを恐れるあまり不利な条件で取引を続けるため、経営は薄利で苦しかったという。自社の裁量でできることも少なく、人が機械のように深夜まで働いている状況で、いわゆる「きつい・汚い・危険」と呼ばれる3Kの「町工場」から抜け出せない悪循環であった。
そんななか、1977年に勇輝氏の父で現相談役の山本昌作氏が入社した。「世界に冠たるモノづくり大国・日本の底辺を支える熟練の技」―。日本の中小企業を語る際、しばしば耳にする賛辞だが、工場に入った昌作氏が目にしたのは、そんな理想とはかけ離れた、不合理な古い慣行が闊歩する世界だった。
あるとき、職人に円筒形の部材を削って円すい状の台形へと加工してもらった。見ていると、刃物台を傾けながら延々2時間にわたって初めから終わりまで同じ調子で少しずつ削り続けていた。「最初は粗く削り、最後の微妙なところだけ注意しながら削ればもっと早く削れるはずだ」と昌作氏は思った。こんなこともあった。職人が円盤状の部材に6カ所の穴を均等に開けている。その作業を見ていると、数十キログラムの回転テーブルを据え付け、時間をかけて芯出しをして最初の穴を開け、そこから360度を6で割っておのおのの穴を開けていた。「三角関数を使えば簡単にできる。たいそうな道具まで使って滑稽なことをやっているなあ」。
一事が万事だった。昌作氏は疑問が生じるたびに「なぜそうするのか」と問うて回った。説明に納得できず、質問を繰り返すと職人は次第に不機嫌になっていく。「うるさい」「グズグズ言わず目で盗め」。そして最後には「オレにもわからへんのや」「こうやれと言われてきたのや」と音を上げた。
「『日本は職人の国』『技術立国』などといわれますが、一種の神話のようなものではないでしょうか。確かに価値ある技術を持った職人もいて、マスメディアなどで取り上げられますが、同一人物が何度も紹介されるケースがよくあります。職人の大半は、たいしたことでもないことを、言われた通り、しきたり通りやっているに過ぎません。理屈を解き明かし知恵を絞るという姿勢は希薄だというのが現場の実感です」(昌作氏)
③ 打った手と成果
度重なるコストカットの要求で人が機械のように働いている状況を打破すべく、同社は売上げの8割を占めていた自動車メーカーとの取引を打ち切り、大量生産をやめ多品種少量生産に特化した。人の成長を目的とし、毎回新しいものに挑戦することで、よりクリエイティブな仕事をするためだ。感覚と我慢で仕事をする職人が支配する工場から、知恵を絞って楽しく働ける場所にするという昌作氏の挑戦が本格化し始めた。
1980年代に入りマイクロプロセッサーを使用したコンピューター(マイコン)が登場し、1982年に量産化が始まった。昌作氏はこれに目を付けた。目指すはマイコンと工作機械とのオンライン化。すなわちマイコンによる機械加工の数値制御だ。それまで、工作機械をコントロールするためのデータは、もっぱら紙テープに開けたパンチ穴で機械に伝えられた。このテープを鑽孔(または穿孔)テープと呼び、通常は1列中の8個の穴の有無で「0」「1」の信号を記録する。
昌作氏は「マイコンも鑽孔テープも言語は一緒。オンライン化できるはず」と考えたが、FAメーカーは「できない」の一点張り。自力でやるしかないと腹をくくった同氏は、大阪のソフトウエア会社を2週間かけて探し回った。そのなかの1社が応じてくれたが途中で挫折。さらに会社を探してようやくオンライン化に成功した。これにより4畳半の保管庫いっぱいの鑽孔テープのロールが5インチのフロッピーディスク1枚に収まった。保管庫の棚から段ボール箱を下ろして目的のテープを探すという骨の折れる作業も不要になった。またフロッピーのデータは上書きができるため、データ変更も容易となった。
オンライン化と並行して職人が個々のやり方で行っていた作業の標準化と、業務全般のデータベース化を進めた。ただ、熟練者の技術を定量化するのはそう簡単ではない。例えば刃物の選定、刃物で削るときの回転数、切り込み量、刃物で削る送りスピードなど、加工するための条件がいくつもある。こうした職人技を1つ1つ定量化しなければならない。また、熟練者1人1人に製造工程のなかで「なぜその加工条件が重要なのか」を聞き出し、暗黙知を理解しながら定量化する必要がある。だが同じ製品の加工でも、職人によって答えがバラバラ。それぞれが経験や勘を頼りに加工するためやり方が違う。行き当たりばったりでたまたま成功したやり方を「正しい」と思い込んでいる職人もいる。そうした個人の経験に偏った情報を聞き出し、バラバラな意見をすり合わせて最適化を進めた。
1年かけてデータベース化を終えると、プログラムをつくり実際に機械を稼働させる段階に入っていく。昌作氏は社員に「プログラムをつくり、機械を始動させたら帰宅せよ。工場に残るな」と命じ、1年半にわたり社員が会社に残っていないかどうかをチェックした。とはいえ、今のようにシミュレーションソフトなどがない時代。すんなりいくはずがない。翌日、出社した社員が見たものは、折れた刃物、引きちぎられたネジ、部品の締め付け工具まで黙々と削っている機械だった。毎朝のように繰り広げられる悲惨な光景に、社員から「こんなこと、もうやめましょう」という大合唱が起きたのは当然だった。
「ここが勝負どころだ」。昌作氏は社員を説得するため語りかけた。「1週間で折れた刃の金額を全部足していくらになる?五万円じゃないか。1日6時間無人化し、それを1週間続けたほうが得でしょう」と。実際には20万円の締め具が破損したり、機械が大破して300万円の修理費がかかったりしたこともあったが、ずっと下請けを続けてジリ貧になるよりましだった。「へこたれるな!」。自身にも社員にもそういい聞かせ続けた。
こうして、職人の技術やノウハウを定量化し、その最適値をデータベース化し、人が昼間につくったプログラムで機械が夜働き、多品種少量を受注から5日(リピートなら3日)で納品する「HILLTOP System」【図表5‐19】が出来上がった。このシステムを活用することで、通常は5軸加工機のプログラミング習得に約5年かかるところを、製造知識のない文系の新入社員でも約3カ月で習得することが可能になったのである。
さらに工作機械を稼働させる際の安全確認も仕組み化した。加工手順書のデータを読み込ませるだけで加工環境をバーチャルシミュレーション上で再現するシステムを自社開発した。このシミュレーションの特長は、多品種少量でも瞬時に加工環境を再現し、若手社員でも簡単に安全確認が可能になった点である。また、バーチャル上でシミュレーションを流すため、プログラマーは工作機械の前で安全確認を行う必要がなくなった。これにより米国法人の工場にある工作機械に、日本で組んだプログラムのデータを送信して遠隔稼働させることも可能だ。そして、加工工程をデータベース化することで、リピート注文が来た際には人の記憶に頼らずすぐ対応できる。そのため社員はルーティン作業から解放され、毎回新しいものに挑戦することで、よりクリエイティブな仕事に集中できる。機械が24時間無人稼働で製品を作り、多品種少量生産を短納期で納品する。これが他社との大きな差別化ポイントになっている。
④ 学ぶべき成功のポイント
現在、同社には売上構成比が30パーセントを超える取引先はない。「30パーセントを超えると自分で決められなくなる」(昌作氏)。図面をもらわなければ仕事ができないような、顧客任せの下請け企業ではない。開発、企画、設計、デザインの段階からモノづくりに関わり、提案する「サポーティングインダストリー」を標榜する。パートナーは自動車、半導体、医療などあらゆる業種に広がり、そこからの受注の8割が1、2個という数量である。このスタイルで利益が出せるのは、夜間も休日も無人で働く機械と、それを稼働させる社員のモチベーションとスキルの高さゆえだ。
取引依存度の高い上得意先や、売上構成比の上位を占める少数の売れ筋商品に頼るのではなく、その他のあまり売れない商品やニッチな商品の販売量を積み重ねて全体の売上げを確保する。消費者、生産者、出品者をオンライン上で結ぶことで、ボリュームゾーン(売れ筋商品)だけに頼らず少量でニッチなニーズもすくい取るというビジネスモデルは「ロングテール」と呼ばれ、アマゾンやネットフリックスなどが採用していることでも知られる。同社が展開する多品種少量生産は、こうしたロングテール戦略の製造業版といえる。コスト競争力が求められる量産品ではなく、数は少ないが技術力を強く求められ、開発プロセスになくてはならない「試作品」という領域を主戦場とする一方、月当たり約3000品種に及ぶ試作品を短納期で提供し、米国法人では北米を中心に海外市場へ販路を拡大するまでに成長した。
同社には「楽しくなければ仕事じゃない」とのポリシーがある。昌作氏は、町工場の時代から「油まみれとは無縁な、白衣を着て働く工場にする」という夢を持っていた。それを実現するための取り組みが、職人技の定量化であり、多品種少量生産であり、24時間無人稼働の実現であった。人の仕事が「ルーティン作業」から「人には人にしかできないクリエイティブな業務」にシフトすれば、新しい事業を生み出すための時間を創出することもできる。現在、同社は自動搬送用ロボットや錠剤検査装置など、部品加工事業から装置開発事業、ソフトウエア開発事業へとそのフィールドを広げている。
金属加工を手掛ける企業が数多くあるなか、同社は多品種少量生産かつ短納期で提供するという難しいサービスを、加工技術・作業工程の最適化・データ化・標準化によって属人化を防ぎ、誰もが簡単に加工プログラムを組めるようにすることで実現した。このHILLTOP System により多品種少量生産の24時間無人稼働が可能となり、ライバルが敬遠する仕事も受注し、それが次の受注を生んでいる。自社の現状を捉えた上で、どのような工場になりたいかという「夢」をしっかり持ち、製造工程を見直す。その上で自社はどこを尖らせるかを明確にし、そこに向けて徹底的な最適化・データ化・標準化を進めたことが同社の成功要因である。ありたい姿に向けDXを推進し、成果をさらなる発展に振り向ける。こうした「善循環」を回し続けることが重要なのだ。
▼クリックで拡大します
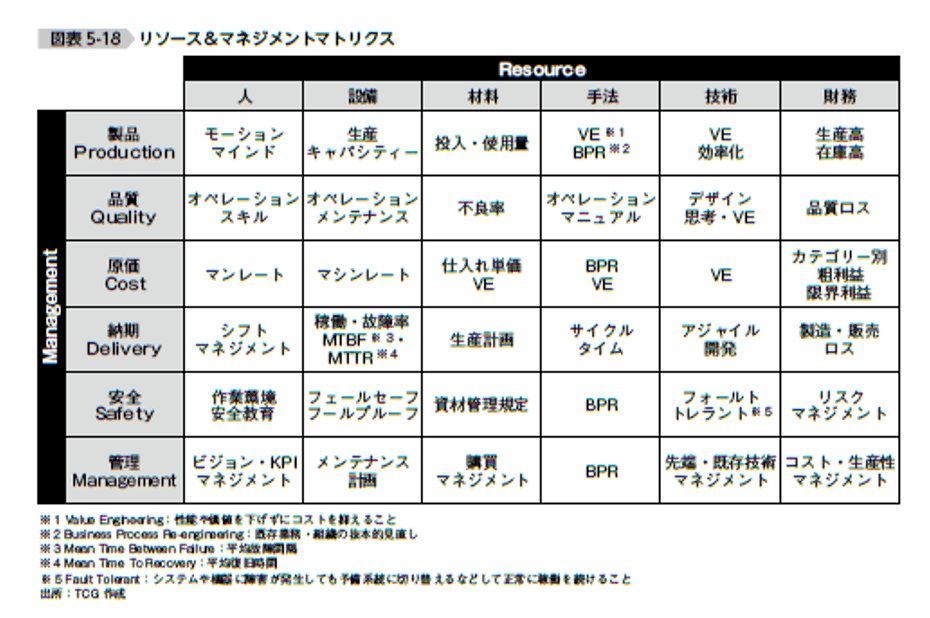
▼クリックで拡大します
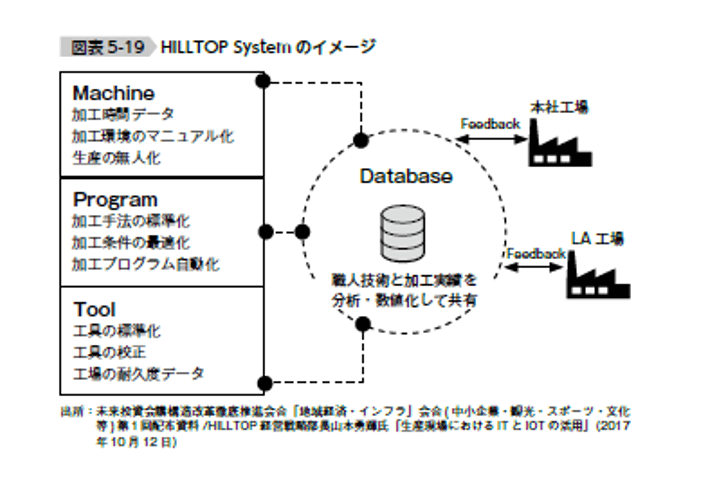
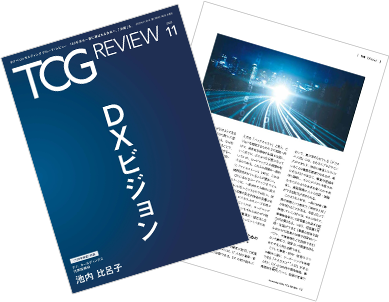
「自社がDXを通じて何を目指すのか」というビジョンからDX戦略を描き、実践すべき改革テーマへ落とし込むメソッドを提言します。
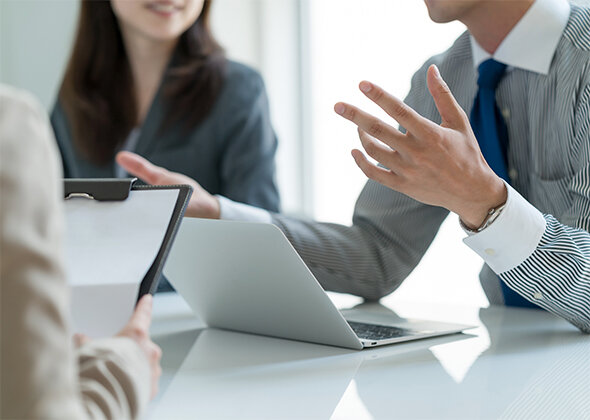